برای تولید فولاد نیاز است که با اعمال گرمای یا دیگر روشهای ممکن مورد نیاز آهن را به نقطه ذوب رساند و این فرایند تنها با استفاده از کوره های ریخته گری ممکن است. در واقع از کوره های ریخته گری برای ذوب آهن یا دیگر فلزات استفاده میشود و این تجهیزات نقش بسیار مهمی را در صنایع فولادی ایفا میکنند. موضوع قابل توجه این است که از زمان شکلگیری صنعت فولاد تا به امروز از انواع مختلف کوره های تولید فولاد رونمایی شده است و هر یک از این کوره های ریخته گری ویژگیهای منحصر به فرد خود را دارند.
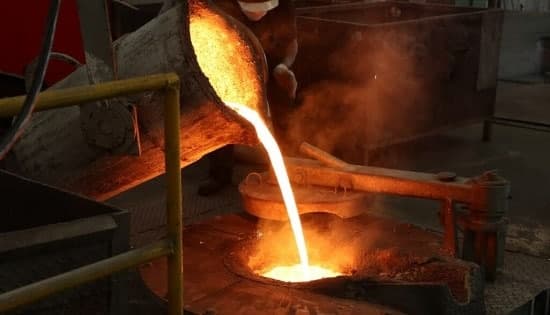
به همین دلیل در این مقاله از تصمیم گرفتیم به معرفی انواع کوره های مورد استفاده در ریخته گری بپردازیم و موارد استفاده از هر یک از آنها در فرایند تولید فولاد را مورد بررسی قرار دهیم. پس اگر شما نیز به دنبال شناخت بهتر انواع کوره های ریخته گری هستید، تا انتهای این مقاله با ما همراه باشید.
کوره تولید فولاد چیست؟
قلب هر کسب و کار فعال در حوزه ذوب و فولاد، کوره ریخته گری است. کوره به دستگاهی اطلاق میشود که برای ایجاد گرامایش در دمای بالا در فرایندهای صنعتی و متالوژی مورد استفاده قرار میگیرد.
کورهها از فناوریهای مختلفی استفاده میکنند که آلیاژ فلز و مواد افزودنی را به درجات خاصی از فولاد تبدیل میکند. برج خنک کننده چیست ؟برج خنک کننده یا کولینگ تاور (Cooling Tower) دستگاهی است که گرمای بوجود آمده در فرآیندها، ماشین ها و دستگاه های صنعتی را از آب در حال جریان دریافت و از طریق تبخیر آن را به اتمسفر انتقال می دهد و مجدداً آب خنک را به سیستم برمی گرداند
موضوع مهم این است که کوره های ریخته گری در انواع مختلفی تولید میشوند که هر یک از آنها ویژگیهای منحصر به فرد خود را دارند. به همین دلیل لازم است به شکل مناسبی با انواع مختلف کوره های تولید فولاد آشنایی پیدا کنید تا بتوانید به شکل بهینهتری از آنها استفاده کنید.
انواع مختلف کوره های ریخته گری کداماند؟
به طور کلی کوره های تولید فولاد در انواع مختلفی تولید میشوند و هر یک از آنها با هدف خاصی مورد استفاده قرار میگیرد. در ادامه به معرفی 4 مورد از رایجترین کوره های تولید فولاد میپردازیم:
-
کوره کوپلا
کوره کوپلا یکی از قدیمیترین و در عین حال رایجترین انواع کورهها است که در زمینه ریخته گری آهن مورد استفاده قرار میگیرد. کوره کوپلا یک کوره استوانهای شکل بلند است که بدنه اصلی آن از یک پوسته فولادی ساخته شده است.
اما جهت جلوگیری از آسیب دیواره داخلی به دلیل گرما و اصطحکاک بالا، داخل آن با آجرهای نسوز پوشانده شده است. عموماً از کوره ریخته گری کوپلا برای ذوب فلزات مختلف بهویژه فلزاتی که دارای ناخالصی هستند، استفاده میشود و شما میتوانید سالها از این کوره استفاده کرده و به کمک آن حجم زیادی از فولاد را بهراحتی تولید کنید.
-
کوره قوس الکتریکی
یکی دیگر از کوره های تولید فولاد محبوب در میان صنعتگران به ویژه صنعتگران فعال در زمینه بازیافت فولاد، کوره قوس الکتریکی است. در این کوره از سه میله کربنی عمودی بهعنوان الکترود بهمنظور ایجاد قوس جهت تولید گرمای لازم برای ذوب استفاده میشود و بدین ترتیب مواد قرار گرفته در محفظه گرمایشی در یک دمای مناسب ذوب میشوند.
کوره قوس الکتریکی امکان بازیافت %100 ضایعات فلزی را دارد و به دلیل انعطافپذیر بودن فرایند این امکان را به کارخانههای ذوب میدهد تا هر زمان که تمایل داشتند فرایند را شروع کرده یا متوقف نمایند. برج خنک کننده خشک به برج خنک کننده ای می گویند که در داخل آن کویل های فین دار به کار رفته است.
-
کوره اجاق روباز
کوره روباز نیز یکی دیگر از کورههای پرکاربرد در صنایع فولادی است. در کوره روباز، کربن اضافی و سایر ناخالصیهای آهن خام برای تولید فولاد سوزانده میشوند. در واقع روش کار با این نوع از کوره ریخته گری به این شکل است که ضایعات آهن در کوره ریخته شده و کربن حاصل از آهن به گاز مونوکسید کربن تبدیل میشود.
بدین ترتیب ناخالصیها از آهن خام جدا شده و مذاب آهن با میزان کربن موردنظر تشکیل میشود. فرایند تولید فولاد در کوره روباز کند است و همین موضوع باعث میشود که اپراتور تسلط بیشتری روی فرایند داشته باشد.
-
کوره القایی
همانطور که از نام این نوع از کوره تولید فولاد مشخص است، در کوره های القایی از فناوری القایی با جریان های الکتریکی متناوب جهت اعمال گرمای موردنیاز برای ذوب فلز استفاده میکند. این روش در مقایسه با 2 نمونه کوره قبلی از مزایای بیشتری برخوردار است و شما نیازی ندارید مثل کوره کوپلا از سیستم احتراق استفاده کنید یا مثل کوره قوس الکتریکی، یک قوس ایجاد کنید و تمام فرایند با القای میدان مغناطیسی دنبال میشود.
به همین دلیل نیز کوره های تولید فولاد القایی در حال حاضر صنعت تولید فولاد را در اختیار خود گرفته است. نحوه استفاده از این کوره ها آسان بوده و محصولات تولیدی آنها نیز از کیفیت بالایی برخوردار است.
-
کوره بوته
کوره های بوته ای قدیمی ترین نوع کوره های تولید فولاد به شمار میروند. کوره های بوته برای ذوب و نگهداری دسته های کوچک آلیاژهای غیر آهنی استفاده می شود. در این کوره ها از مواد نسوز برای ساخت قالب استفاده شده است و به همین دلیل نیز میتواند دمای بالایی را که برای ذوب محصولات فلزی مختلف نیاز است را تحمل کند. این کوره امکان ذوب مقادیر کمی از فلزات را فراهم کرده است و به همین دلیل نیز در مجتمعهای صنعتی بزرگ چندان مورد استفاده ندارد.
امروزه کوره های ریخته گری یکی از ارکان اصلی در تمامی صنایع به ویژه صنایع فولادی به شمار میروند. تفاوتی هم نمیکند که دقیقاً چه کسبوکاری در چه ابعادی باشد. هر کسبوکاری که در آن نیاز به ذوب فلزات احساس میشود، ملزم به داشتن یک کوره ریخته گری برای این منظور است.
به همین دلیل در این مقاله تلاش کردیم برخی از رایجاگرچه که مهارت، اصلیترین فاکتور در انجام هر کاری است، اما بدون ابزار و امکانات مناسب، ماهرترین افراد نیز در کار خود دچار مشکل میشوند. بهعنوانمثال، یک آشپز برای تهیه غذای خوب به ظروف مناسب نیاز دارد. به همین ترتیب، یک ریختهگر نیز برای دستیابی به قطعات باکیفیت، نیازمند استفاده از کوره ذوب مناسب است.
انتخاب کوره ریخته گری نامناسب حتی ممکن است فرآیند ریختهگری را بهطورکلی مختل کند. چراکه فلزات مختلف به دلیل تنوع در خواص فیزیکی و شیمیایی، نیازمند این هستند که در کوره مخصوص به خود ذوب شوند. در ادامه به بررسی مهمترین انواع کوره های صنعتی ذوب آهن و فولاد میپردازیم.
چگونه کوره ذوب مناسب انتخاب کنیم ؟
در هر دو روش ریختهگری قالب دائمی و ریختهگری قالب موقت، عامل مشترک، فلزمذاب است. در عملیات کلی ریختهگری، فلزمذاب در داخل قالبهای ریختهگری ریخته میشود. این تهیه فلز مذاب باید بهموقع در محلهای ریختهگری انجام شود. بنابراین، یک سایت تولیدی که عملیات ریختهگری را انجام میدهد، باید دارای کورههای مخصوص برای تأمین فلز مذاب برای عملیات ریختهگری باشد. با در این لینک آشنا شوید.
انواع مختلفی از کورههای ذوب وجود دارند که در کارخانههای ریختهگری موجود هستند. انتخاب کوره ذوب مناسب بسیار مهم است و نیازمند توجه به پارامترهای مختلفی است که بهطور مستقیم با فلز موردنظر برای ذوب، ارتباط دارند. علت جلبک زدن برج خنک کننده چیست ؟جلبک در برج خنک کن به دلیل املاح و مواد مغذی در آب ، دما و نور مناسب به وجود می آید و سیستم توزیع آب را دچار مشکل خواهد کرد.
در مرحله انتخاب کوره ذوب و ریخته گری مناسب، پارامترهای مهم عبارتاند از:
- نوع فلز یا آلیاژ فلزی که ریختهگری میشود
- دمای ذوب فلز یا آلیاژ
- مقدار حرارت تولیدی یا حداکثر دمای کوره
- مقدار سوخت مصرفی کوره
- الزامات و محدودیتهای محیط زیستی
- ظرفیت تولید کارخانه
- هزینه سرمایهگذاری سیستم کوره ذوب انتخابی
- هزینههای نگهداری و عملیاتی کوره
انواع کوره ذوب فلزات کدام اند ؟
رایجترین کورههای ذوب آهن و فولاد که در اکثر کارخانهها مورداستفاده قرار میگیرند شامل کوره بوتهای، کوره کوپلا، کوره القایی و کوره الکتریکی میشوند. هرکدام از این کورهها، تکنولوژی منحصربهفرد خود را دارند که آنها را برای شرایط و ظرفیتهای تولیدی متفاوت مناسب میکند.
علاوه بر کورههای یادشده که برای ذوب فلزات بهمنظور ساخت قطعات استفاده میشوند، کورههای دیگری نیز وجود دارند که برای استخراج فلزات از سنگ معدن آنها به کار برده میشوند. این کورهها شامل کوره رو باز، کوره بسمر، کوره اکسیژن قلیایی و کوره بلند میشوند که اغلب برای آهنسازی و تولید فولاد مورداستفاده قرار میگیرند. در مقاله ، با این کورهها و روشهای فولادسازی بیشتر آشنا شوید.
کوره بوته ای
کورههای بوتهای اغلب برای ذوب آلیاژهای غیرآهنی که نقطه ذوب پایینی دارند به کار برده میشوند. مکانیزم این کورهها نیز شامل استفاده از یک پاتیل سرامیکی نسوز است تا در هنگام مواجهه با دمای بالا، بتوانند مقاومت کنند. این پاتیل سرامیکی که بوته نام دارد، در بالای منبع حرارت قرار میگیرد تا فلز و مواد افزودنی موجود در آن ذوب شود. اندازه این بوتهها متفاوت است.
این نوع کوره ذوب دارای ساختار محصور شده است تا حرارت در درون آن نگه داشته شود. سوختهای مصرفی رایج برای کوره بوتهای نیز شامل زغالسنگ یا گاز طبیعی میشوند. در طراحی و سیستم گرمایش کورهها نیز تفاوتهایی وجود دارد. بهغیراز کورههای بوتهای متحرک و ثابت، کورههای بوتهای کج و ثابت نیز وجود دارند. همچنین باید بین کورههای مقاوم در برابر گرمایش و گرمایش با سوخت تفاوت قائل شد.
انواع کوره بوته ای رایج در صنایع ریختهگری عبارتاند از:
- کوره بوتهای ثابت: پاتیل درون این نوع کوره ثابت است و فلز مذاب با استفاده از یک شیر در کف کوره از آن خارج میشود.
- کوره بوتهای متحرک بالابر: زمانی که فلز داخل بوته کاملاً ذوب شد، پاتیل را با کمک جرثقیلهای داخل محل تولید بالا میبرند تا فلز مذاب به قالبها برسد.
- کوره بوتهای کج: پاتیل درون کوره ثابت است و کل سیستم کوره کج میشود تا فلز مذاب از آن خارج شود.
مزایا و معایب کوره بوته ای
از مزایای کوره ذوب بوتهای میتوان به هزینههای سرمایهگذاری پایین و بهرهبرداری و نگهداری ساده آن اشاره کرد. علاوه بر این، امکان ذوب مقادیر کمی فلز و تغییر سریع محتویات بوته نیز وجود دارد. بااینحال، کورههای بوتهای برای ذوب مقادیر زیاد از فلزات و آلیاژها مقرونبهصرفه نیستند، زیرا مصرف انرژی بهشدت افزایش مییابد و عملیات دستی بسیار زمانبر میشود.