در دنیای مدرن تولید، فناوری های پیشرفته ای نظیر فرزکاری (CNC Milling) و تراشکاری (Turning) نقش اساسی در فرآیندهای تولید دارند. هدف از این مقاله، مقایسه این دو روش مهم و بررسی نقاط قوت و ضعف هر یک از آن ها است. با مطالعه این متن، خوانندگان با ویژگی های خاص فرزکاری و تراشکاری آشنا خواهند شد و می توانند تصمیمات بهتری در انتخاب روش مناسب برای پروژه های خود بگیرند. همچنین، در این مقاله به تفاوت های کلیدی در دقت، سرعت تولید، و نوع مواد قابل استفاده در هر یک از این فرآیندها خواهیم پرداخت. در نهایت، این بررسی به تولیدکنندگان و مهندسان کمک می کند تا با درک بهتر از این دو روش، به بهینه سازی فرآیندهای تولید خود بپردازند.
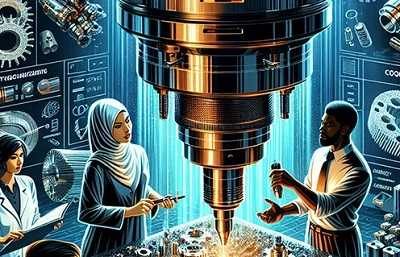
تعریف و اصول پایه فرزکاری و تراشکاری
تعریف فرزکاری (CNC Milling)
فرزکاری یا CNC Milling به فرآیند ماشین کاری اطلاق می شود که در آن از یک ابزار برش دوار برای حذف مواد از یک قطعه کار استفاده می شود. این فرآیند معمولاً برای تولید قطعات با دقت بالا و اشکال پیچیده به کار می رود. در فرزکاری CNC، ماشین ها به صورت خودکار و با برنامه نویسی کنترل می شوند که این امر باعث افزایش دقت و کاهش خطاهای انسانی می شود. فرزکاری به طور گسترده ای در صنایع مختلفی مانند خودروسازی، هوافضا و تولید تجهیزات پزشکی کاربرد دارد.
تاریخ فرزکاری به اوائل قرن بیستم برمی گردد که اولین ماشین های فرزکاری به صورت دستی ساخته شدند. با پیشرفت فناوری، ماشین های CNC توسعه یافتند و امکانات بیشتری برای برنامه ریزی و کنترل دقیق فرآیند فراهم کردند. این ابزارهای مدرن قابلیت تولید قطعات با دقت میکرونی را دارند و به این ترتیب نیازهای صنعتی را به بهترین شکل ممکن برآورده می کنند.
تعریف تراشکاری (Turning)
تراشکاری یا Turning به فرآیند ماشین کاری دیگری اشاره دارد که در آن قطعه کار به دور محور خود می چرخد و ابزار برش ثابت بر روی آن حرکت می کند. این روش معمولاً برای تولید قطعات استوانه ای یا مخروطی شکل استفاده می شود و به دلیل سادگی و سرعت بالای آن در تولید انبوه، محبوب است. تراشکاری می تواند به صورت دستی یا با استفاده از ماشین های CNC انجام شود که در هر دو حالت، دقت و کیفیت بالا را ارائه می دهد.
تاریخچه تراشکاری به گذشته های دور برمی گردد که از ابتدا به عنوان یکی از قدیمی ترین روش های تولید قطعات در نظر گرفته می شد. با پیشرفت فناوری، ماشین های تراش CNC به بازار آمدند که امکان کنترل دقیق و اتوماتیک فرآیند را فراهم می کنند. این نوع تراشکاری به ویژه در صنایع تولیدی و ساخت قطعات بازیافت و نگهداری تجهیزات بسیار مورد استفاده قرار می گیرد.
اصول پایه و نحوه عملکرد هر دو روش
اصول پایه فرزکاری و تراشکاری بر اساس حذف مواد از قطعه کار استوار است، اما نحوه عملکرد هر یک از این دو روش متفاوت است. در فرزکاری، ابزار برش به صورت دوار عمل می کند و می تواند همزمان از چندین جهت به قطعه کار فشار وارد کند. این ویژگی به فرزکاری اجازه می دهد تا اشکال پیچیده و جزئیات دقیق را ایجاد کند.
برعکس، در تراشکاری، قطعه کار به دور محور خود می چرخد و ابزار برش به صورت خطی بر روی آن حرکت می کند. این روش معمولاً برای تولید قطعات با اشکال ساده تر و استوانه ای مناسب تر است. هر دو روش می توانند در ترکیب با تکنیک های دیگر مانند سنگ زنی (Grinding) و حفاری (Drilling) به کار گرفته شوند تا کیفیت نهایی قطعات بهبود یابد.
انتخاب بین فرزکاری و تراشکاری بستگی به نوع قطعه، دقت مورد نیاز و حجم تولید دارد. در حالی که فرزکاری برای تولید قطعات پیچیده تر مناسب است، تراشکاری معمولاً برای تولید قطعات استوانه ای و سریع تر انتخاب می شود.
مزایا و معایب فرزکاری و تراشکاری
فرزکاری (Milling) به عنوان یک فرآیند ماشین کاری، به دلیل قابلیت های خود در تولید قطعات با دقت بالا و سطحی صاف، مورد توجه قرار گرفته است. یکی از مزایای اصلی این روش، توانایی آن در ایجاد اشکال پیچیده و هندسه های خاص است. فرزکاری به کاربر این امکان را می دهد که با استفاده از ابزارهای مختلف، برش های مختلفی را بر روی مواد مختلف از جمله فلز، چوب و پلاستیک انجام دهد. همچنین، سرعت بالای این روش موجب افزایش بهره وری در خطوط تولید می شود و می توان به راحتی عملیات شبیه سازی و برنامه ریزی را انجام داد.
علاوه بر این، فرزکاری قابلیت تولید قطعات با ابعاد دقیق و تکرارپذیری بالا را فراهم می کند. این ویژگی به ویژه در صنایع خودروسازی و هوافضا که نیاز به دقت بسیار بالایی دارند، از اهمیت ویژه ای برخوردار است. همچنین، تنوع در ابزارهای فرزکاری و قابلیت تغییر آن ها، موجب افزایش انعطاف پذیری در تولید می شود.
معایب فرزکاری
با وجود مزایای فراوان، فرزکاری نیز معایبی دارد که باید در نظر گرفته شوند. یکی از معایب اصلی این روش، هزینه بالای تجهیزات و نگهداری آن هاست. ماشین آلات فرزکاری معمولاً نیاز به سرمایه گذاری اولیه بالایی دارند و هزینه های تعمیر و نگهداری نیز می تواند به مرور زمان افزایش یابد. به علاوه، فرزکاری معمولاً به نیروی کار ماهر و متخصص نیاز دارد که خود موجب افزایش هزینه ها می شود.
همچنین، فرزکاری ممکن است در برخی موارد زمان بیشتری نسبت به سایر روش های ماشین کاری مانند تراشکاری (Turning) برای تولید یک قطعه نیاز داشته باشد. این امر به ویژه در تولید قطعات با حجم بالا می تواند به عنوان یک عامل محدودکننده عمل کند. تولید ضایعات در فرزکاری می تواند بالاتر از سایر روش ها باشد که این موضوع نیز باید مورد توجه قرار گیرد.
مزایای تراشکاری
تراشکاری یکی از روش های قدیمی و موثر در ماشین کاری است که تسلط بر فرآیند آن، می تواند به تولید قطعات دقیق و با کیفیت منجر شود. یکی از بزرگترین مزایای تراشکاری، توانایی آن در تولید قطعات استوانه ای و گرد است که در صنایع مختلفی مانند خودروسازی و تولید ماشین آلات کاربرد دارد. این روش به دلیل سادگی و کارایی خود، برای تولید قطعات با ابعاد بزرگ و حجم های بالا مناسب است.
تراشکاری همچنین می تواند با سرعت بالا انجام شود و در بسیاری از موارد، هزینه های تولید را کاهش دهد. این امر به ویژه در تولید انبوه قطعات با طراحی های مشابه، موجب صرفه جویی در زمان و هزینه می شود. علاوه بر این، ابزارهای تراشکاری معمولاً عمر طولانی تری دارند و نیاز به تعویض کمتری نسبت به فرزکاری دارند.
معایب تراشکاری
با وجود مزایای تراشکاری، این روش نیز معایبی دارد که باید در نظر گرفته شوند. یکی از معایب اصلی آن، محدودیت در تولید اشکال پیچیده است. تراشکاری معمولاً برای تولید قطعات با اشکال ساده و استوانه ای مناسب است و در تولید اشکال غیرمنظم و پیچیده با چالش هایی مواجه می شود. این موضوع می تواند در برخی صنایع که نیاز به طراحی های خاص دارند، یک نقطه ضعف محسوب شود.
علاوه بر این، تراشکاری معمولاً نیاز به نیروی کار ماهر دارد و این امر می تواند به افزایش هزینه های تولید منجر شود. همچنین، تولید ضایعات در این فرآیند نیز ممکن است به اندازه فرزکاری بالا باشد. زمان لازم برای تنظیم و آماده سازی ماشین آلات تراشکاری ممکن است بیشتر از فرزکاری باشد که این موضوع می تواند به کاهش بهره وری در برخی موارد منجر شود.
مقایسه دقت و کیفیت تولید
دقت در فرزکاری به معنای توانایی ماشین فرز (Milling Machine) در تولید قطعات با ابعاد و شکل های دقیق است. این فرایند شامل استفاده از ابزار برش چرخشی است که به قطعه کار فشار می آورد و آن را به شکل دلخواه برش می دهد. دقت در فرزکاری به عوامل مختلفی بستگی دارد، از جمله نوع ابزار، سرعت برش، و نوع مواد اولیه. فرزکاری نسبت به دیگر روش های تولید، مانند تراشکاری، توانایی بیشتری در تولید سطوح پیچیده و هندسه های غیرمعمول دارد. همچنین، استفاده از تکنولوژی های جدید مانند CNC (Computer Numerical Control) در فرزکاری به افزایش دقت و کاهش خطاهای انسانی کمک کرده است.
دقت در تراشکاری
تراشکاری (Turning) فرآیندی است که در آن قطعه کار به دور محور خود می چرخد و ابزار برش ثابت به آن فشار می آورد. دقت در تراشکاری به عواملی نظیر تنظیم مناسب ماشین، نوع ابزار استفاده شده و شرایط محیطی بستگی دارد. یکی از مزایای تراشکاری، قابلیت تولید قطعات استوانه ای و گرد با دقت بالا است. با استفاده از فناوری CNC در تراشکاری، می توان دقت بالایی را در تولید قطعاتی با ابعاد دقیق و کیفیت سطح مطلوب به دست آورد. این روش همچنین امکان تولید انبوه قطعات را با حفظ دقت مطلوب فراهم می کند.
کیفیت نهایی محصولات
کیفیت نهایی محصولات به مجموعه ای از ویژگی ها و مشخصات اشاره دارد که عملکرد، دوام و زیبایی آنها را تعیین می کند. در هر دو روش فرزکاری و تراشکاری، کیفیت نهایی تحت تأثیر عوامل متعددی قرار می گیرد. در فرزکاری، سطوح نهایی ممکن است به دلیل نوع ابزار، سرعت برش و متریال مورد استفاده متغیر باشد. در تراشکاری، کیفیت سطح نهایی به نوع ابزار، عمق برش و سرعت چرخش قطعه کار بستگی دارد. به طور کلی، استفاده از ماشین آلات پیشرفته و فناوری های نوین در هر دو روش، موجب بهبود کیفیت نهایی محصولات و کاهش نواقص می شود. انتخاب روش تولید مناسب بستگی به نیازهای خاص پروژه و مشخصات مورد نظر دارد.
سرعت تولید و زمان بندی فرآیندها
سرعت تولید در فرزکاری به میزان کارایی و سرعتی که ماشین های فرز قادر به انجام فرآیند برش هستند، اشاره دارد. این سرعت تحت تأثیر عواملی همچون نوع مواد اولیه، ابزارهای مورد استفاده، و پارامترهای ماشین کاری قرار می گیرد. به طور کلی، فرزکاری به دلیل قابلیت انجام عملیات پیچیده تر و دقت بالاتر در مقایسه با برخی روش های دیگر، به عنوان یکی از فرآیندهای اصلی در صنعت ماشین کاری شناخته می شود. در این فرآیند، سرعت برش (Cutting Speed) و نرخ پیشروی (Feed Rate) از جمله پارامترهای کلیدی هستند که بر سرعت تولید تأثیر می گذارند. با افزایش این پارامترها، می توان به تولید سریع تر و کارآمدتر دست یافت، اما باید توجه داشت که این افزایش ممکن است منجر به کاهش کیفیت سطح کار و عمر ابزار شود.
سرعت تولید در تراشکاری
تراشکاری به عنوان یکی دیگر از روش های ماشین کاری، به فرآیند شکل دهی و برش مواد چرخانده شده اشاره دارد. سرعت تولید در این روش نیز به متغیرهایی چون نوع قطعه کار، نوع ابزار و تنظیمات ماشین بستگی دارد. در تراشکاری، سرعت دوران (Spindle Speed) و نرخ پیشروی از عوامل مهمی هستند که بر روی کیفیت و سرعت تولید تأثیر مستقیم دارند. به طور معمول، در تراشکاری می توان با تنظیمات مناسب و انتخاب ابزار مناسب، سرعت تولید را به حداکثر رساند. همچنین، در این فرآیند، به دلیل چرخش قطعه کار، امکان ایجاد اشکالاتی مانند عدم تعادل در حرکات و افزایش حرارت وجود دارد که باید به دقت مدیریت شوند تا از کاهش کیفیت قطعه جلوگیری شود.
تأثیر زمان بندی بر هزینه ها
زمان بندی مناسب در فرآیندهای ماشین کاری، نقش بسزایی در کنترل هزینه ها دارد. با بهینه سازی زمان تولید، می توان هزینه های مربوط به نیروی کار و نگهداری ماشین آلات را کاهش داد. در هر دو فرآیند فرزکاری و تراشکاری، زمان تولید به طور مستقیم بر روی هزینه نهایی محصول تأثیر می گذارد. به عنوان مثال، اگر زمان تولید در فرزکاری به طور مؤثری مدیریت شود، می توان به تولید انبوه و کاهش هزینه های مربوط به تولید دست یافت. از سوی دیگر، عدم زمان بندی مناسب می تواند منجر به تاخیر در تحویل و افزایش هزینه های اضافی شود. بنابراین، انتخاب روش های مناسب زمان بندی و کنترل دقیق فرآیندها برای به حداقل رساندن هزینه ها ضروری است.
نوع مواد قابل استفاده در هر روش
فرزکاری (Milling) یک فرآیند ماشین کاری است که در آن از ابزارهای برش چرخشی برای شکل دهی به مواد استفاده می شود. مواد مناسب برای فرزکاری معمولاً شامل فلزات نرم و سخت، پلاستیک ها و چوب هستند.