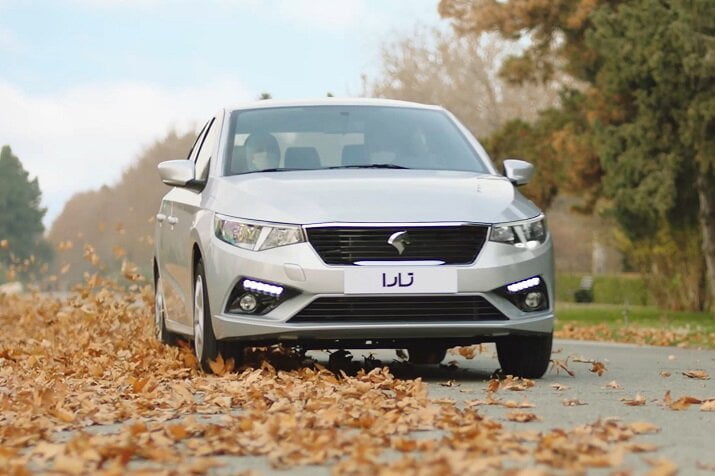
گروه صنعتی ایران خودرو در گزارش امروز (یکشنبه) خود به دو مورد اشاره کرده است: تولید انبوه اتوبوس های آمبولانس ساخت داخل و از طرف دیگر تولید قالب های 25 ستاره و صرفه جویی در هزینه روپیه.
به گزارش مخبران ، ایران خودرو دیزل قول داد که نمونه اولیه خودرو را ظرف سه ماه از توافق قبلی که بین اورژانس این کشور و بزرگترین خودروساز تجاری خاورمیانه منعقد شده بود تحویل دهد ، اما با تلاش گروهی از کارشناسان ، این پروژه در سال 35 راه اندازی شد. روز و تولید انبوه آن آغاز شد.
به همین ترتیب ، اولین اتوبوس آمبولانس در ایران دارای یک شاسی یک تکه بود که می توانست 9 تخت بیمارستان را در خود جای دهد. این اتوبوس آمبولانس از یک موتور قدرتمند OM457 با قدرت 350 اسب بخار استفاده می کند و همچنین دارای یک توالت فرنگی ، یک جعبه پزشکی اورژانس کامل و سایر امکانات و تجهیزات برای روز آمبولانس است.
ایران خودرو دیزل با داخلی سازی محصولات و استفاده از توانایی تولید کنندگان داخلی در تکمیل این محصول ، کاهش چشمگیری در ارزش هر اتوبوس آمبولانس ایجاد کرده است.
همچنین ، در قسمت دیگری از گزارش ایران خودرو ، بزرگترین خودروساز این کشور با مشارکت تیم مهندسی ساپکو و تولیدکنندگان داخلی ادعا کرده است که 25 محور برخی از قطعات خودروی ستاره ای را بومی سازی کرده و 600000 دلار صرفه جویی کرده است. برای اولین بار در کشور ، قسمتهایی از آمپ داشبورد جلو آمپ داشبورد ، فرمان با کلیدهای کنترل و قاب تشکیل دهنده فرمان طراحی و بومی سازی شدند.
این 15 نوع قالب ، از جمله قالب های تزریق پلاستیک ، ریخته گری رنگ منیزیم و قالب های قاب و فوم ، توسط شرکت های غالب در زنجیره تأمین ایرانی خودرو داخلی سازی می شوند. با این حال ، همه این اشکال از زمان تاسیس ساپکو از آلمان ، فرانسه ، پرتغال ، ایتالیا ، کره و چین تهیه شده اند.
مزایای اصلی داخلی سازی قالب های محور جلو آمپ داشبورد ، فریم های روی فرمان (MFC) با فریم های کنترل روی آمپ داشبورد ، هزینه تست این قالب ها را در خارج از کشور کاهش می دهد ، سهولت تغییرات مهندسی و زمان اجرا را تا زمان شما کاهش می دهد دریافت انتقادات و پیشنهادات.
همچنین ، با بومی سازی دانش قطعات مورد اشاره ، کلیدهای کنترل صدا با پایه های لازم برای ساخت قالب قطعات و کروز کنترل اتومبیل فراهم می شوند.
انتهای پیام